Here comes ~ Guan Yu Da Power internal lean management teacher class again! Master Zou Jianmin from Jingxinzhi lecturing "Plan Upward Revision" of "Ten Sharp Tools for On-site Improvement" series courses
2022.05.10
The first course of Lean Management "Use lean Techniques" : 10 tools to eliminate waste
One, the site ten waste
Two, twelve big action waste
Three, site improvement ten sharp tools
On April 15, 2022, the second course of Lean Management teacher "Plan Upgrade" was officially delivered. As one of the series courses of "Ten Sharp tools for on-site improvement", Zou Jianmin analyzed the case to more than 100 students on site and explained the key points of the class.
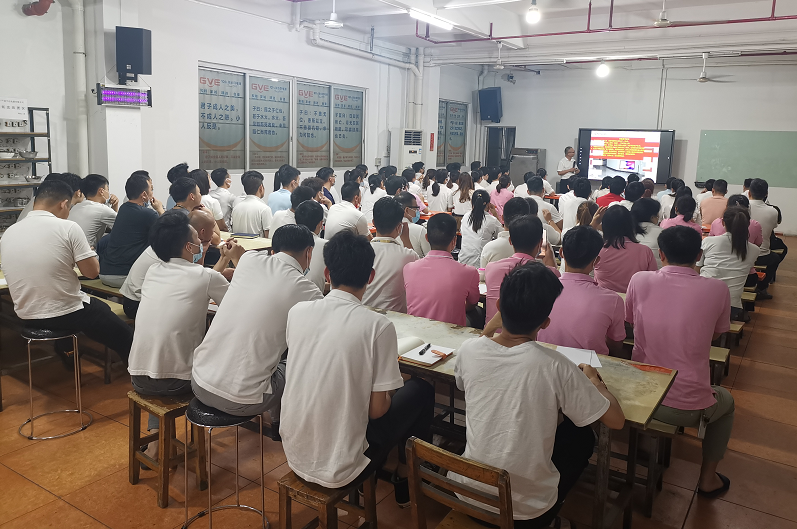
Mr Zou shared several key points:
First, why do [plan upward]?
An enterprise is in beginning stage, workshop space is huge, product is onefold, working procedure is simple, equipment is less, its planar graph often is relatively reasonable, through thoughtful cooked slightly.
But with the increase of products, the extension of the process, the acquisition of equipment, as well as the increase of the whole sales, its site will appear a chaotic situation, at this time there are a lot of unreasonable phenomenon appeared, so that the product and the workpiece in the production of transportation route is too long, which is the hidden danger of manufacturing waste every time.
So the floor plan needs to be replanned and adjusted every once in a while.
Ii. Adjustment purpose
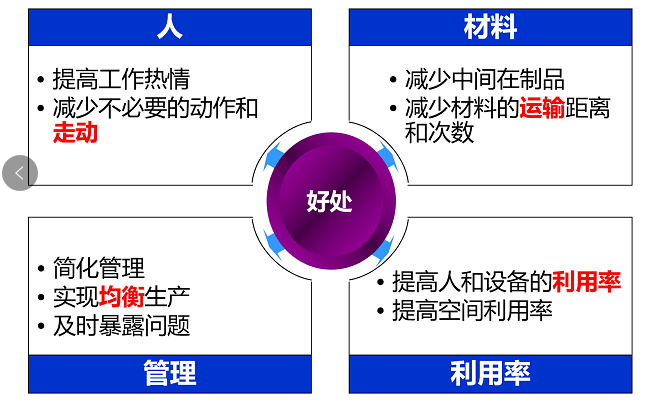
3. Steps of plant planning
1, capacity planning decomposition
2. Process optimization
3. Line body layout design
4. Standard operation planning
5. Warehousing and logistics distribution
6. Tour paths
7. Supporting humanities
8. Lean operation management
Four, the type of workshop layout

5. Unitized layout
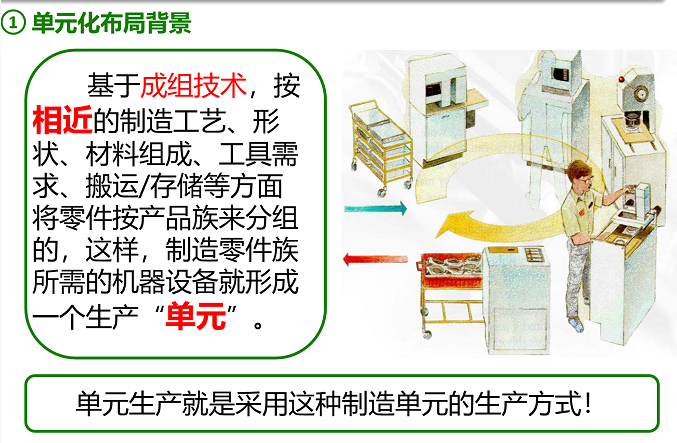
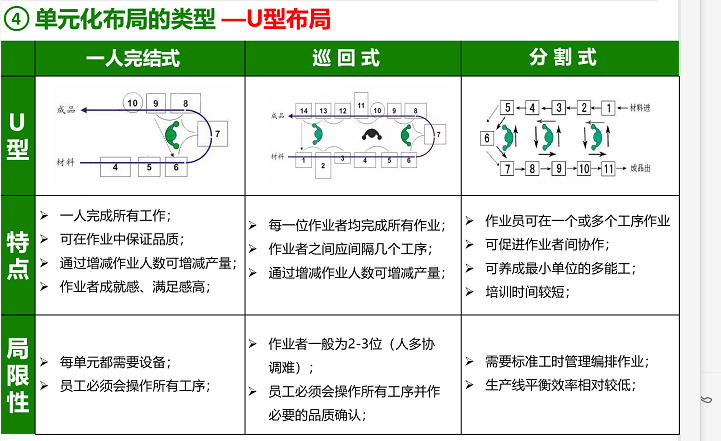
Six, lean layout principles:
1. One flow principle
2. The principle of safety satisfaction
3, the shortest distance principle
4. Principle of space utilization
5. Flexibility principle
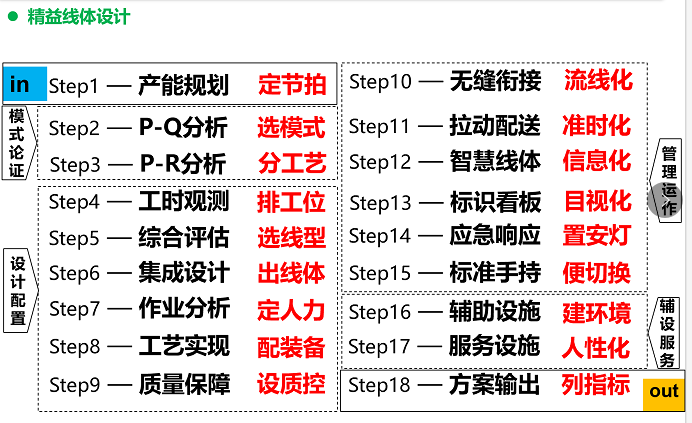
7. Improvement steps of Lean layout:
1, according to the process, draw the current layout map
2. Determine the analysis object according to the product family
3. Actual logistics route analysis (current situation animation demonstration)
4. Collect and analyze key information in the process
5. On-site inventory analysis
6. Draw lean layout map (demonstrate it several times with animation)
7. Compare the old and new layout structures
8. Develop detailed implementation plans
In the end, Mr. Zou arranged homework for the class: write or draw the logistics status quo of guan Yuda partners' own work place. The partners responded positively and quickly submitted their answers to the class.
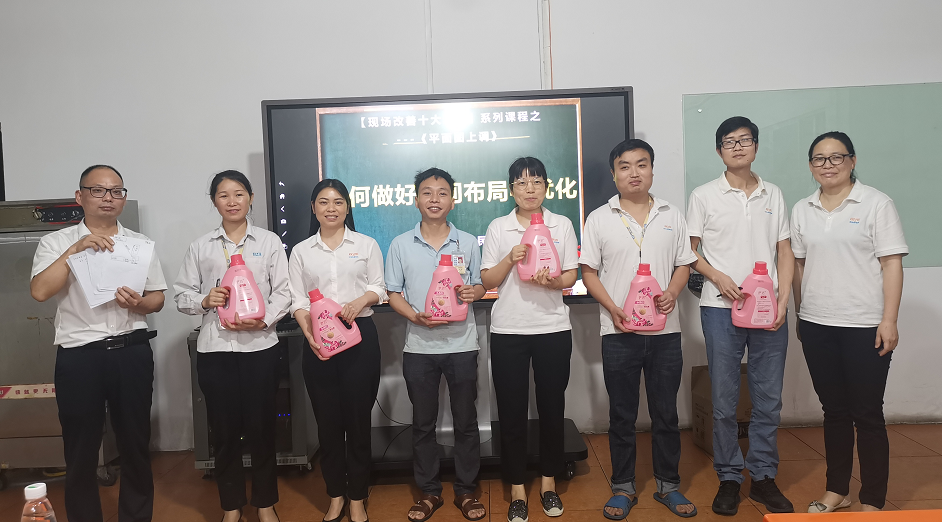
Author: Liu Qiongqing
One, the site ten waste
Two, twelve big action waste
Three, site improvement ten sharp tools
On April 15, 2022, the second course of Lean Management teacher "Plan Upgrade" was officially delivered. As one of the series courses of "Ten Sharp tools for on-site improvement", Zou Jianmin analyzed the case to more than 100 students on site and explained the key points of the class.
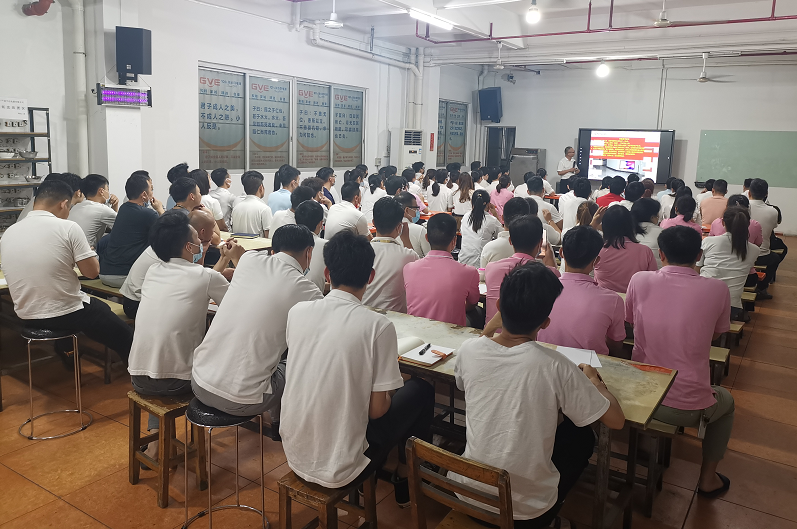
Mr Zou shared several key points:
First, why do [plan upward]?
An enterprise is in beginning stage, workshop space is huge, product is onefold, working procedure is simple, equipment is less, its planar graph often is relatively reasonable, through thoughtful cooked slightly.
But with the increase of products, the extension of the process, the acquisition of equipment, as well as the increase of the whole sales, its site will appear a chaotic situation, at this time there are a lot of unreasonable phenomenon appeared, so that the product and the workpiece in the production of transportation route is too long, which is the hidden danger of manufacturing waste every time.
So the floor plan needs to be replanned and adjusted every once in a while.
Ii. Adjustment purpose
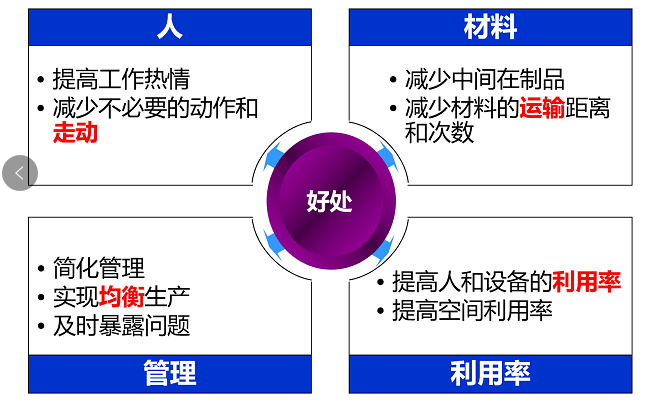
3. Steps of plant planning
1, capacity planning decomposition
2. Process optimization
3. Line body layout design
4. Standard operation planning
5. Warehousing and logistics distribution
6. Tour paths
7. Supporting humanities
8. Lean operation management
Four, the type of workshop layout

5. Unitized layout
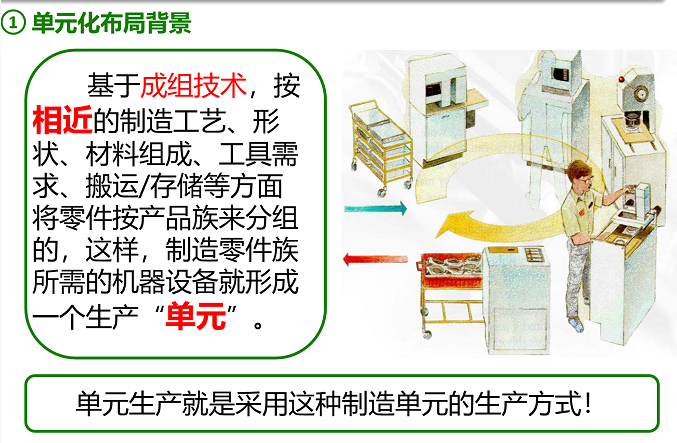
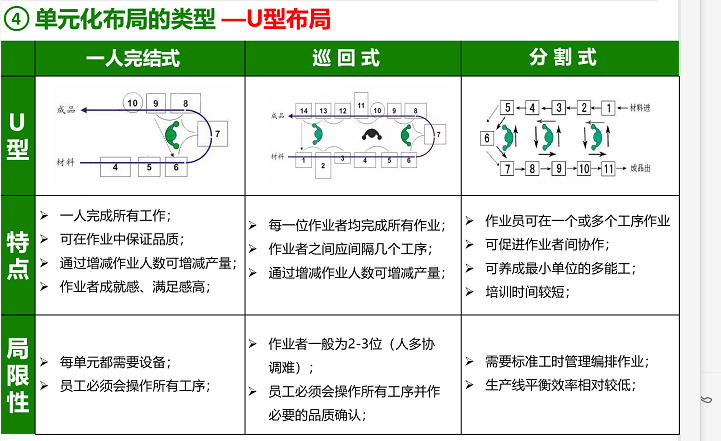
Six, lean layout principles:
1. One flow principle
2. The principle of safety satisfaction
3, the shortest distance principle
4. Principle of space utilization
5. Flexibility principle
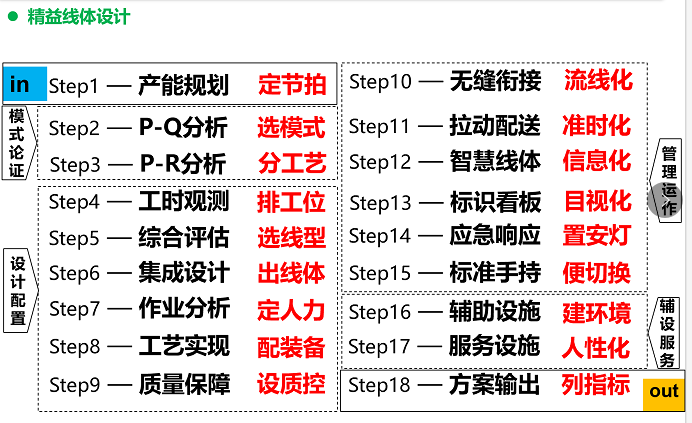
7. Improvement steps of Lean layout:
1, according to the process, draw the current layout map
2. Determine the analysis object according to the product family
3. Actual logistics route analysis (current situation animation demonstration)
4. Collect and analyze key information in the process
5. On-site inventory analysis
6. Draw lean layout map (demonstrate it several times with animation)
7. Compare the old and new layout structures
8. Develop detailed implementation plans
In the end, Mr. Zou arranged homework for the class: write or draw the logistics status quo of guan Yuda partners' own work place. The partners responded positively and quickly submitted their answers to the class.
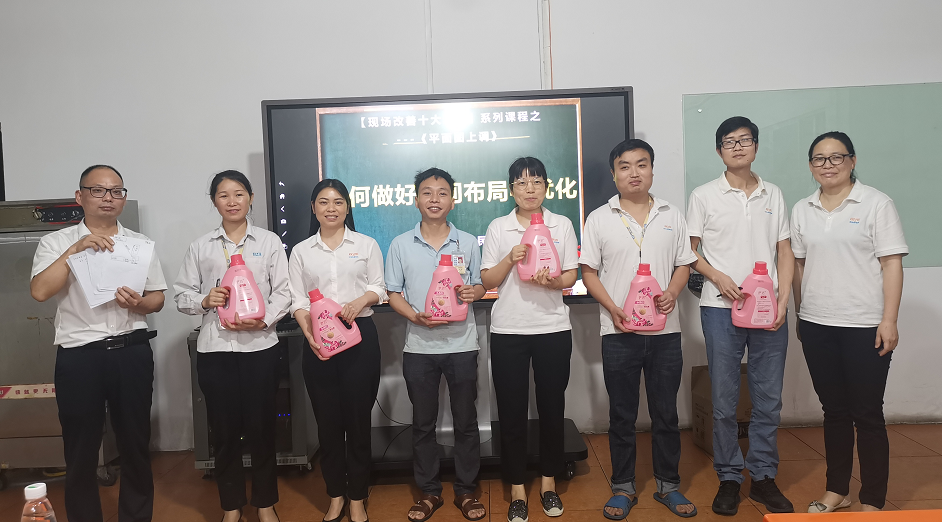
Author: Liu Qiongqing